Battery Inspection and Development with CT Scan Data Analysis – Volume Graphics.
Advanced software from Volume Graphics helps manufacturers detect flaws, improve safety, and reduce development costs.
Automotive battery designers are intently focused on understanding the complex chemistry and construction of Lithium-ion batteries. The same can be said for their manufacturers, who must continuously monitor production processes to ensure that battery cells, packs, and modules adhere to specifications. After all, a vehicle’s driving range, time needed to recharge, and long-term battery performance must all be optimized and any safety risks mitigated before the BEV revolution can reach maximum cruising speed.
Industrial Computed Tomography, more commonly referred to as CT scanning, has begun playing a significant role in all these endeavors. So has the advanced software that makes sense of CT-generated images, allowing users to measure voids and particle sizes within electrode active material during the research and development phase, detect delamination and contamination during cell manufacturing, analyze electrical connections and electrolyte fill levels, and provide many other quality-assurance functions that were once impractical or even impossible to perform.
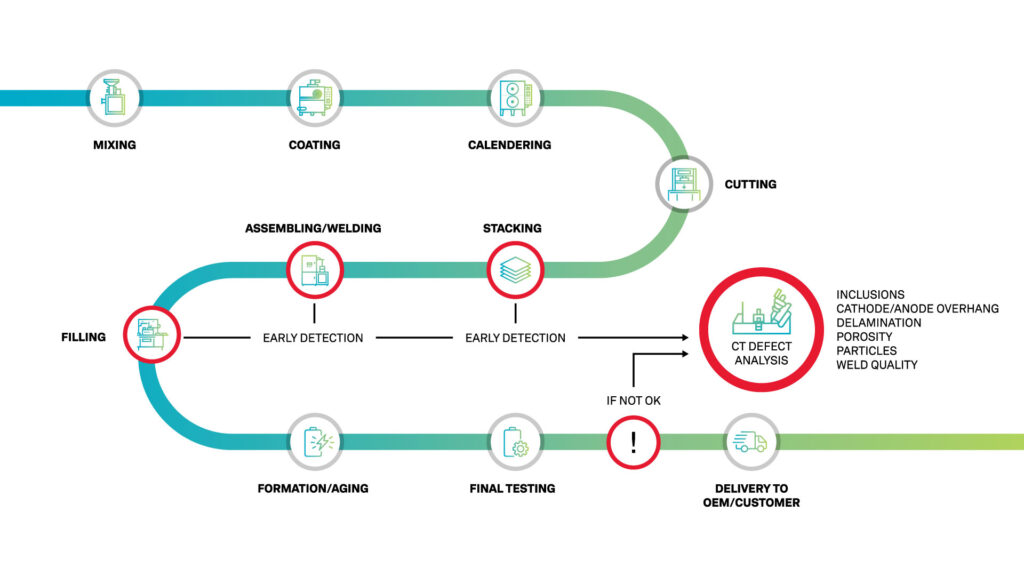
Beyond the black and white
🔥 What about we co-host a webinar? Let's educate, captivate, and convert the battery economy!
Batteries News is the global go-to online magazine for the battery industry, we can help you host impactful webinars that become a global reference on your topic and are an evergreen source of leads. Click here to request more details
Although CT scanning is the only metrology tool able to non-destructively inspect for these and countless other defects and conditions, there’s one caveat: analysis of the resulting data is complex and requires advanced software analysis to interpret the images and identify various features.
These software tools can dramatically simplify the inspection process, allowing even non-expert users to leverage CT scanning to its fullest capability. This is especially true for battery researchers, designers, and manufacturers, who have a host of application-specific tools at their disposal.
For example, VGSTUDIO MAX from Volume Graphics allows operators to identify metallic inclusions that can damage the electrode separators. They can verify that anode overlap is sufficient to prevent short-circuits and do so at any point in the manufacturing process, even once the battery pack has been completely assembled. More importantly to the future of BEVs—and indeed any electromechanical device that requires a battery—is the ability to optimize existing designs, evaluate new materials, and possibly develop storage technologies that would completely revolutionize the industry.
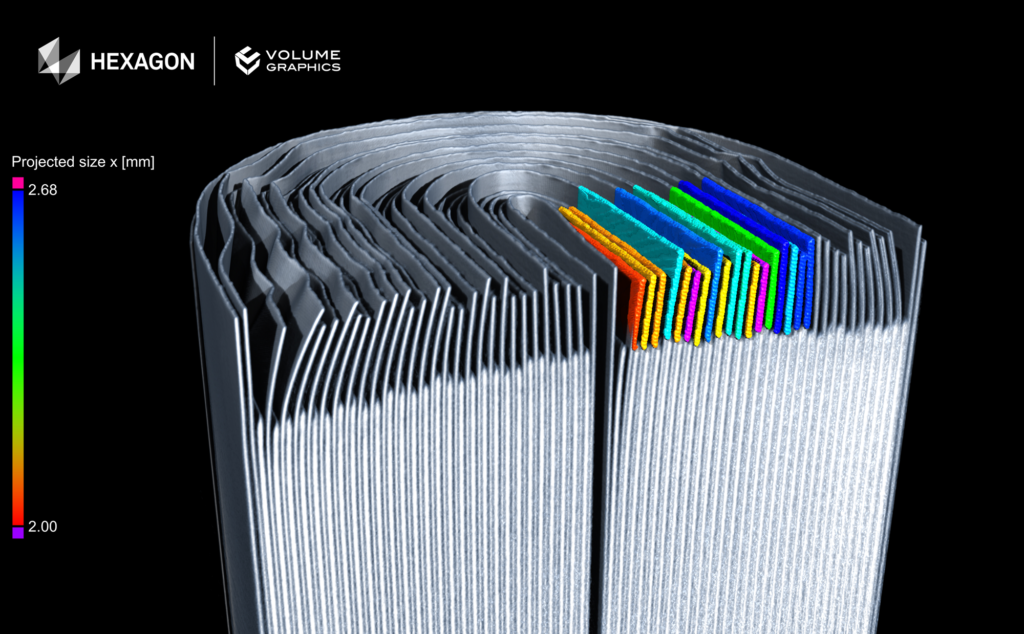
New software capabilities expand analysis scope
Volume Graphics has introduced several new tools, such as an anode overhang analysis function that provides enhanced visualization and reporting for this common measurement. There’s also a new auto-segmentation feature that allows the operator to digitally “paint” a representative section of a structure they wish to analyze, after which the software will identify and mark any like structures.
One of the most exciting of these is a machine-learning function that automates much of the effort that comes with image processing. Customers can train the software on which part-features or details to look for and what to do with them when found. For instance, the computer could reference previously saved models in the Paint & Segment function just described, thus automating the segmentation process to detect undesired foreign particles within a battery cell.
Given the growing demand in the e-mobility sector, such capabilities will quickly go from nice-to-haves to must-haves. Most countries aim to phase out internal combustion engines by 2040 at the latest (and some have far more aggressive plans), which means that hundreds of factories worldwide will be called upon to produce safe, efficient, and cost-effective batteries in quantities never seen.
Sections of this article originally appeared in EV Design & Manufacturing.
Unlock the power of 3D data analysis with Volume Graphics software. Start your FREE 4-week evaluation for VGSTUDIO, VGSTUDIO MAX, and VGMETROLOGY. Discover the difference Volume Graphics can make for your business today!
About Volume Graphics
Volume Graphics, part of Hexagon, is a global leader in the development of software for non-destructive testing based on industrial computed tomography (CT). Customers around the world across all manner of applications and industries use our software for quality assurance in product development and production. Visit volumegraphics.com to learn more.
Hexagon is a global leader in digital reality solutions. Learn more about Hexagon (Nasdaq Stockholm: HEXA B) at hexagon.com and follow us @HexagonAB.
Contact: Reda Belarbia – Volume Graphics E-Mobility/Batteries Practice
Email: reda.belarbia@hexagon.com
For further information, please visit:
Battery Inspection and Development – Applications – volumegraphics.com
READ the latest Batteries News shaping the battery market